Supply Chain Disruptions and Shortages: The Domino Effect That Keeps Getting More Complicated
Photo by Charl Folscher on Unsplash
If you are a business on the receiving end of recent supply chain delays, you’re not alone. Everyone from e-commerce retailers and brick-and-mortar outlets to healthcare facilities and service industries has felt the bite of disruptions and shortages over the last year. Logistics professionals are also not immune from the economic consequences of these delays. What’s really happening and why aren’t you receiving the merchandise or supplies you need? Here’s an overview of the situation. It’s more complex than many people realize and often fuels itself, making slow downs and shortages even more aggravating as time goes on.
How the Initial Pandemic Wave Started Delays
An increase in demand that precipitated a feedback loop
The delays we are experiencing now in winter of 2022 actually began in 2020 with the onset of the coronavirus pandemic. Multiple factors aligned to produce a shift in spending patterns:
- Illness and caring for family members
- Local business closures
- Border crossing restrictions
- Political unrest
As a result, consumers moved from spending money on services to spending on goods. For instance, in place of eating out and going to the movies, the average person invested in gourmet foods and home entertainment systems. When it was deemed too risky to go to the doctor’s office, people bought home heart monitors and pulse oximeters. No vacation this year? Let’s remodel the kitchen instead.
The longer people remained at home abstaining from activities and not participating in travel and entertainment experiences, the more discretionary income they had available to make purchases. Additionally, consumers who anticipated shortages increased their bulk buying to forestall running out of essential items.
These trends, plus the direct impact of the pandemic itself, resulted in shortages and shipping delays in many sectors. It was the start of a feedback loop that would continue into 2021 and beyond.
Photo by Wesley Tingey on Unsplash
Events of 2021 That Exacerbated Hold Ups and Shortages
The cascade of delays broadens
As we entered 2021, the preference for goods over services continued, but the new cyber shopping created in 2020 out of necessity, safety, and convenience was increasingly fraught with headaches and further delays. Imagine supply chain disruptions and shortages as an array of dominos, only this isn’t a single line of tiles where hitting one knocks over one more, and so on. Instead, it’s like one of those Ultimate Domino Battles, with entangled loops that look like snakes eating their own tails.
New Covid variants and long Covid combined to cause work outages across the globe. The shortage of labor was felt everywhere, in manufacturing, shipping, and ports of entry, as well as in end destinations for goods, where there were fewer people available for stocking, managing, and selling inventory. On top of those conditions, which produced delays and shortages in material goods, we experienced numerous other factors that contributed to the aforementioned feedback loop:
- The “Great Resignation” and strikes over work conditions, wages, and vaccine and mask mandates
- Insufficient freight containers and port container space
- Inadequate warehousing capability where overflow inventory accumulated
- Port congestion, with container ships unable to unload
- Lack of parts for transportation infrastructure (aeronautics, trucking, etc.)
- Unpredictable extreme weather events
As delays continued and shortages grew, both businesses and consumers felt even more compelled to shore up vital goods, which only created more demand, leading to further supply chain chaos.
The Omicron Surge of Late 2021 and Early 2022
Cumulative effects of lost productivity
Enter the Omicron variant at the end of 2021. This virus mutation, which coincided with holiday travel, was significantly more contagious than previous variants. People across the planet fell ill rapidly, in greater numbers than were seen with earlier waves. Omicron resulted in a significant decrease in the global workforce, equivalent to roughly two weeks of lost productivity.
However, the losses due to Omicron didn’t translate to a single two weeks of delays simultaneously worldwide. Rather, each link in any given supply chain suffered its own two-week slow down. The cumulative effect was more like a series of rogue waves, not a tsunami that could be weathered as a discrete event.
As an example of this phenomenon, let’s look at how an order for Battery Management System (BMS) printed circuit boards (PCBs) could take ten weeks longer than expected to arrive at its destination. To start, the BMS PCB supplier needs to wait an additional two weeks for a standard resistor necessary for the board’s manufacture that used to be abundantly available for overnight shipment.
Once the board is complete, it ships four weeks after the initial order. This timeline includes the first two-week delay for the resistor as well as two more weeks caused by backups due to labor shortages.
But the delays don't stop there. The export port is backed up by another two weeks, bringing the end customer’s delay to six weeks … so far. Add two more weeks for the BMS PCB to be unloaded and to clear customs at the port of entry, then be transported by truck (also running behind by two weeks due to a shortage of drivers) to the customer. The total delay equals ten weeks.
The more links in the chain, the longer the delay between order and delivery. And the farther away parts and materials are coming from, the greater the chance that delays will ensue.
Photo by henry perks on Unsplash
Prognosis for the Future
Potential solutions for pain points
Unfortunately, experts predict supply chain disruptions and shortages may continue well into 2022, depending on how we fare with the pandemic, the factors listed above, and clearing backlogs created so far. Therefore, the management of delays is crucial for both B2B and B2C businesses.
Some solutions for ongoing delays include:
- Don’t let inventory run low when possible. Keep inventory management tight, ideally with software that allows for real-time updates.
- Partner with carriers and logistics experts who can help with pain points like order tracking, last mile delivery, fulfillment, and customs brokerage.
- Explore creative manufacturing options (see below).
- Remain agile to reallocate budgets and staffing.
- Supplement regular goods and services with online services and digital products.
- Adjust pricing to accommodate export shipping changes.
- Maintain transparency with customers. For many, the ambiguity of delivery is more stressful than a late arrival date they know they can rely on.
Keep a close eye on current events. There’s a chance that the easing of Covid restrictions and trajectory of the pandemic could permit a reduction in supply chain disruptions and shortages later this year. However, there are no guarantees, and we've seen the pandemic take a turn for the worse just as everyone assumed it was winding down.
Reshoring Your Supply Chain
Weather unknowns with greater security
Given the uncertainty of what lies ahead and the likelihood of continued delays with offshored supply chains, there is another major solution to consider. Reshoring your supply chain can reduce lead time and improve certainty, which gives business owners better customer service that also translates to cost savings and improved peace of mind.
Two years ago, Rose Batteries did just that by moving to a hybrid supply chain model that melds US-based operations with assembly in Mexico using the maquiladora program to manufacture battery packs in Mexico. Originally bolstered under NAFTA and reinforced with the United States-Mexico-Canada Agreement (USMCA), the maquiladora system allows for the tax- and duty-free importation of raw materials and components into Mexico for assembly there, followed by the exportation of finished goods back to the US.
This gives us multiple benefits, specifically low labor costs and vastly reduced supply chain barriers, while still maintaining our American headquarters, with no worries about language barriers or complex negotiations with third parties. It's a lean model that can be especially helpful for small companies with limited staff available for the full-time management of supply chain logistics.
Our internal nearshoring efforts have been so successful, in fact, that our customers have sought out our expertise in this area. Now we not only provide this service for clients needing battery engineering, manufacturing, and assembly, but we also advise companies interested in embracing this model too.
Whether your business needs help with electronics assembly or wants to explore reshoring its supply chain using the maquiladora program, Rose Batteries welcomes the opportunity to speak with you. We're certain that our turnkey approach to supply chain management will help your business withstand the unknowns of 2022 and beyond. Feel free to reach out at your convenience and let us know how we can assist.
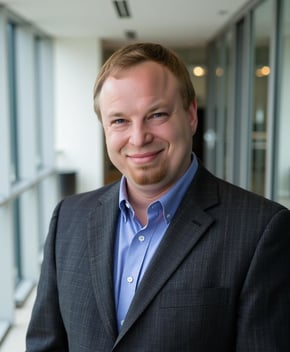