Welcome to our comprehensive guide on battery manufacturing essentials.
In today’s fast-paced technological landscape, the demand for reliable and efficient power solutions is greater than ever. Whether you’re new to the field or an experienced professional, this guide equips you with the knowledge needed to navigate the complexities of battery production successfully.
1. Cell Selection:
Cell selection lies at the heart of battery innovation. Manufacturers meticulously evaluate battery cells based on several pivotal factors:
- Capacity: Determines charge storage and delivery capabilities.
- Energy Density: Dictates efficiency in space-constrained applications.
- Lifecycle: Ensures durability and longevity.
- Cost Considerations: Underpin economic feasibility.
By mastering cell selection, manufacturers pave the way for delivering power solutions that meet and exceed modern applications' demands, driving innovation and progress across industries.
2. Board Design:
Board design is critical in all but the most basic battery designs..
- Function: PCBs provide electrical connectivity and protection for the cells (over voltage, under voltage, under current, etc.).
- Advanced Options: Fuel Gauging, Communications (cell status, voltage, capacity, etc), Cell Balancing, Temperature reporting/controls, ID configuration, Sleep/Hibernate options, and even mechanical support or flexible options.
- Precision: Meticulous design ensures optimal signal transmission and seamless integration of components.
Through careful board design, manufacturers enhance the reliability and longevity of the battery pack and electronic devices.
3. Enclosure: (including Plastics & Tooling)
In manufacturing, plastics and tooling are vital for shaping physical components.
- Plastics: These versatile materials form the foundation of many modern products and protect the pack from damage.
- Tooling: The art of crafting molds, which define the precise shapes, sizes, and intricacies of plastic parts.
Attention to detail in plastics and tooling ensures consistent quality across all produced components.
4. Certificates
Certifications validate product integrity and compliance with industry standards.
- Quality: They emphasize product excellence.
- Responsibility: Highlight environmental and safety commitments
Achieving certifications demonstrates a dedication to quality and fosters trust among consumers and stakeholders.
5. DFX (Design for Manufacturing):
DFX principles streamline product development by optimizing manufacturing, assembly, and testing.
- Cost Reduction: Incorporating DFX leads to significant savings.
- Efficiency: Enhances product quality and performance.
Adopting DFX empowers businesses to meet high standards while remaining competitive.
6. Scalable Assembly:
Scalable assembly enables flexible production processes.
- Adaptability: Manufacturers can adjust production volumes in response to demand.
- Efficiency: Effective inventory management and reduced lead times boost competitiveness.
Scalable assembly enhances agility and profitability in manufacturing operations.
7. Automation:
Automation leverages advanced systems like robotics, AI, and machine learning to streamline manufacturing.
- Speed: Accelerates production cycles.
- Safety: Enhances workplace safety.
- Scalability: Facilitates rapid response to market changes.
Automation drives sustainable growth and operational efficiency.
8. Testing & Verification:
Comprehensive testing and verification ensure product quality and reliability.
- Verification: Confirms adherence to design specifications.
- Testing: Assesses functionality and performance.
Prioritizing rigorous testing practices maintains high-quality standards and builds consumer trust.
9. Cost Reductions:
Efficiency and cost-effectiveness are essential for financial health.
- Cost Management: Implementing diligent practices ensures sustainable operations.
- Quality Assurance: Achieves savings without compromising quality.
Effective cost-reduction strategies enhance financial stability and service excellence.
The main challenge in battery manufacturing is delivering reliable and efficient power solutions. Missteps like poor cell selection or flawed board design can lead to subpar performance and product failures. Focusing on these elements guarantees exceptional battery performance and service, meeting modern demands and maintaining a competitive edge.
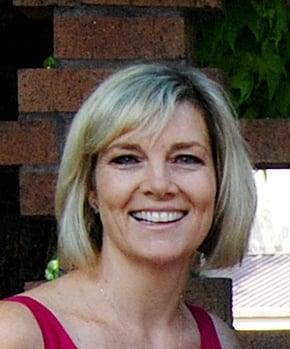